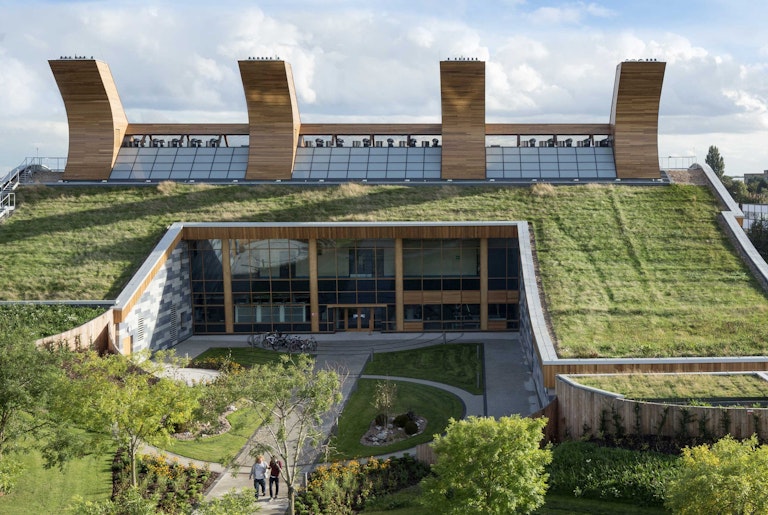
Sustainability
Learn MoreAt Curtins, sustainability is at the core of our approach as we strive to build a better future.
A prototype healthcare module to test and demonstrate innovative construction technologies with the use of innovation practices, for the future of new hospitals in the UK.
Healthcare - The North, England
The Healthcare Sandpit was built as part of the Construction Innovation Hub programme, led by the Manufacturing Technology Centre (MTC). It is a prototype healthcare module adopting the use of innovative construction technologies such as 2D Laser Cut Reinforcement (LCR), robot drilled services and the adoption of a completely pre-cast concrete sub-structure and super-structure.
The project is an opportunity to test and demonstrate the viability of these construction technologies with a view to using the innovation practices on a mass scale for future new hospitals in the UK.
The Healthcare Sandpit is designed to replicate a typical isolation theatre including a gowning room, dirty utility room, clean preparation room and corridor access.
The Sandpit aims to demonstrate a building designed with efficiency in mind. The structural frame consists of three different types of precast concrete members, blade columns, edge beams and slab panels. These repeat at ground-floor and roof levels to ensure structural simplicity and efficiency.
The driver to minimise and simplify the type of pre-cast members manufactured off site was for the Sandpit to showcase that on a large scale this structural solution can take huge advantage of the cost and time saving associated with off-site manufacturing of repeatable elements and just in time site delivery.
To demonstrate a new and unique way for healthcare facilities of the future and to pave the path to a more sustainable way of building these new facilities.
One of the key areas of focus for the Sandpit project was to display the ease and speed of construction, utilising a process focused on MMC whereby much of the construction takes place off-site ready for piecing together on-site. To gain as much as we could from this process, we as the structural engineers ensured that the structural form was kept simplistic with only a few types of members manufactured off site to be delivered to the site when they were needed. On-site time-consuming processes of in-situ shuttering, pouring, and curing, reinforcement tying and stripping were all eliminated along with the inherent errors the in-situ method poses.
At Curtins, sustainability is at the core of our approach as we strive to build a better future.
With a rich history of embracing cutting-edge technology, we lead the way in digital delivery. Accredited with the BSI BIM Level 2 Kitemark, we collaborate in a digital environment using the latest industry tools, and continuously enhance our digital capabilities to add tangible value to our projects.
Let’s talk about your next project and how our experienced team can help
Find your nearest Curtins office
Contact